Rotor blade systems
How many blades should a wind turbine rotor have? Each system has its own characteristics.
Two- and three-bladedrotors
Two- and three-bladed rotors with similar diameters have different surface areas to harvest the three-dimensional turbulent wind field.
Two-bladed rotors compensate for their smaller surface area with a higher tip-speed ratio and use less material to achieve similar power coefficients. High tip-speed ratios require higher running speeds to generate the same mechanical power as lower tip-speed ratios. High operating speeds are non-beneficial to dynamic fatigue loads and noise emissions.
Two-bladed rotors need smaller assembly areas and also have advantages regarding dismantling and maintenance. This, combined with their lower costs, makes two-bladed rotors attractive solutions for some offshore applications in the multi-megawatt range. Most two-bladed wind turbines have downwind rotors.
How the pendulum hub works
Two-bladed rotors are sensitive to the wind shear between the top and bottom of the rotor. Owing to both the tower dam effect and the turbulence behind the tower, two-bladed rotors are subject to a high asymmetric load with lower wind pressure on the bottom blade. This asymmetric load occurs twice with each turn of the rotor, subjecting the rotor blades, hub, drivetrain and tower to dynamic loads.
ESM rubber-metal elements with a star configuration create a ‘pendulum hub’. Thanks to their flexibility, the dynamic load imbalance between the top and bottom rotor blades is absorbed. Stress on adjacent support structures is reduced to the lower residual forces generated by the low stiffness of the deflected rubber elements compared to rigid metal-to-metal fixtures.
Similar decoupling solutions are also possible between three-bladed rotors and hubs.
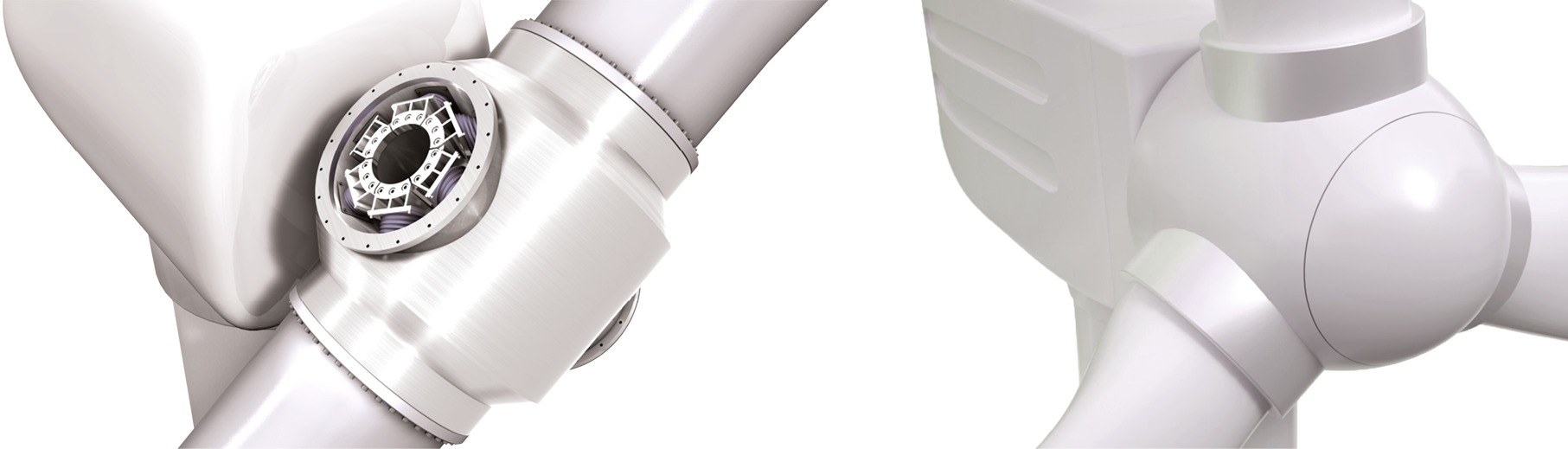
© ESM GmbH